Sustainable Style:
- VTMAG
- Feb 16, 2021
- 7 min read
Updated: Mar 22, 2022
Silver Maple Construction embraces the future of sustainable housing with an extraordinarily innovative and beautiful property in Weybridge
In the rolling hills of Weybridge, Vermont, a striking and sophisticated home stands in the midst of a charming bucolic clearing. As you approach the house from the road, the vibrant color tones of the Douglas Fir wood panels on the outside of the home blend seamlessly with the surrounding mountains and trees. Stepping inside, winsome wooden floors and walls are illuminated by an overabundance of natural light from a long row of tall windows.

Although this fashionable and tasteful home is both smartly appointed and expertly designed, it is by no means the product of lavish expenditure. Silver Maple Construction President Sean Flynn built this two-bedroom/two-bathroom, 1,380 square-foot house at his Weybridge property to serve as the inaugural prototype of Silver Maple’s newest line of affordable pre-fabricated homes. By merging rustic and elegant aesthetics with energy-efficient and cost-effective modern design, Silver Maple Construction has created an iconic contemporary gem in Addison County that serves as an exemplary blueprint for the future of their sustainable housing program.
Sean first started honing his carpentry abilities when he began working as a handyman at Timberlock Resort in Indian Lake, NY at the age of 15. Sean says that the quick learning curve that came with the job incentivized him to develop a wide range of valuable skills at a rapid pace. “It was an incredible opportunity that allowed me to expand my knowledge-base to include a multifaceted range of trade skills. I did a little bit of everything there. I dabbled in guest relations, and I also did some work as a lumberjack, a plumber, and a carpenter. The people who ran the resort were incredibly self-reliant. They really inspired me to pursue a career in building and carpentry. From there, my fascination with building slowly continued to grow. I would take a job from time to time during the years I attended college and also go back to Timberlock to work there in the winter. Over time, I branched out into larger remodeling projects.”

After spending time in a number of different locations in his early adulthood – including a stint in Burlington, Vermont – Sean found his way back to the Green Mountain State in 2001. He then began to work for a high-end builder in the Addison County area by the name of Alex MacDonald. Sean says that the work he did for Alex MacDonald allowed him to “really cut [his] teeth in the world of high-end construction. Working on a team like that helped me to understand what true craftsmanship was. About two years after that, my best friend Mike Steele and I founded Silver Maple Construction together. We started off just as two guys in a pickup truck. These days, we’ve grown the operation to 52 guys in multiple pickup trucks. We’re coming up on our fifteenth anniversary this year in 2021. Through all of the growth, we’ve been able to maintain our reputation by focusing on providing exemplary service and craftsmanship to all of our clients.”
As the proprietor of a highly-rated construction firm that is well known for delivering outstanding results in a timely manner, Sean believes that “true craftsmanship” requires much more than a specialized set of artisan skills. “The way I see it, I know a whole lot of carpenters who can spend years putting together one exquisite piece or project when there are no time limits or cost constraints. Many people can do a fantastic job with that without any real difficulty. I think what defines a true ‘craftsman’ is their ability to produce work at a similar level of quality within the constraints of a budget and a production schedule. That’s what we strive to accomplish with every project that we take on here at Silver Maple Construction. Like any other trade, carpentry – at its essence – is a problem-solving exercise. To be able to create something beautiful, long-lasting and strong in a cost-effective and expedient way, you have to be able to think on your feet and work within the constraints of the job. In theory, a master craftsperson should be able to produce that same level of amazing work within a pace-oriented and goal-driven environment.”
True to that overarching philosophy of expedient craftsmanship, Sean has taken it upon himself to develop a line of aesthetic pre-fabricated homes that will allow Silver Maple Construction to grow their business beyond its current market niche of high-end custom projects. “Most of Silver Maple Construction’s work is in the ‘bespoke’ and ‘high-end’ range, but our new project is really giving us the opportunity to crack the code on what I like to refer to as ‘achievable housing.’ It’s not by any means an entirely new idea, but we’ve been operating in the ‘high-end custom home’ niche for a very long time. Expanding our business portfolio to include these more mass-produced models has proven to be a fascinating learning experience for us.”
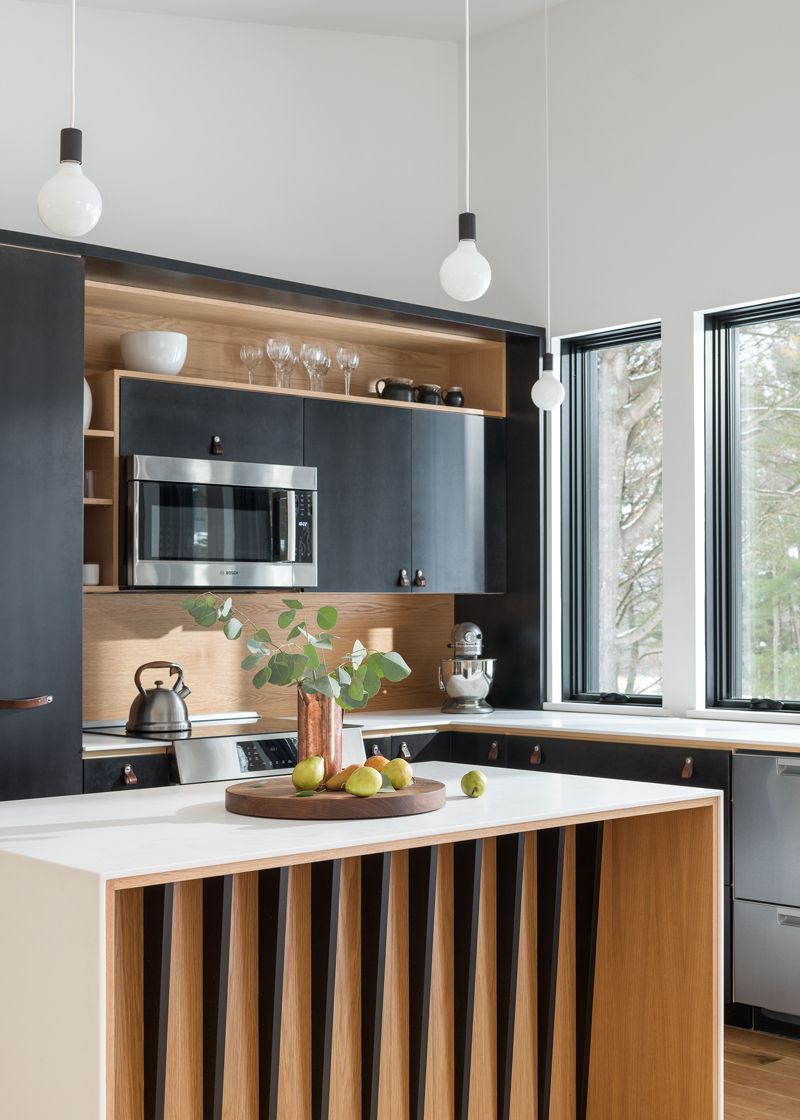
According to Sean, part of the motivation for the recent broadening of Silver Maple Construction’s market focus stems from their recent acquisition of a 30,000 square-foot “panelization” facility. “It’s a huge shop. It’s given us the ability to build all sorts of new structures and components indoors. We decided to leverage our new workshop to incorporate the development of new models of energy-efficient and affordable homes. With the recent housing boom in Vermont, we want to diversify our options to remain flexible as the future unfolds. The idea is to make beautiful, modern, pre-fabricated homes, and then reproduce them many times. The theory is that we will get some interest on a slightly larger scale and be able to expand and pivot into new markets. We’re still in the process of figuring everything out, but we are looking into developing several other different variations – each of which will be ideal for different family situations and price points. By developing low-cost building techniques and standardized home models, we’ll be able to provide our customers with beautifully designed homes that work well with a wide range of budgets.”
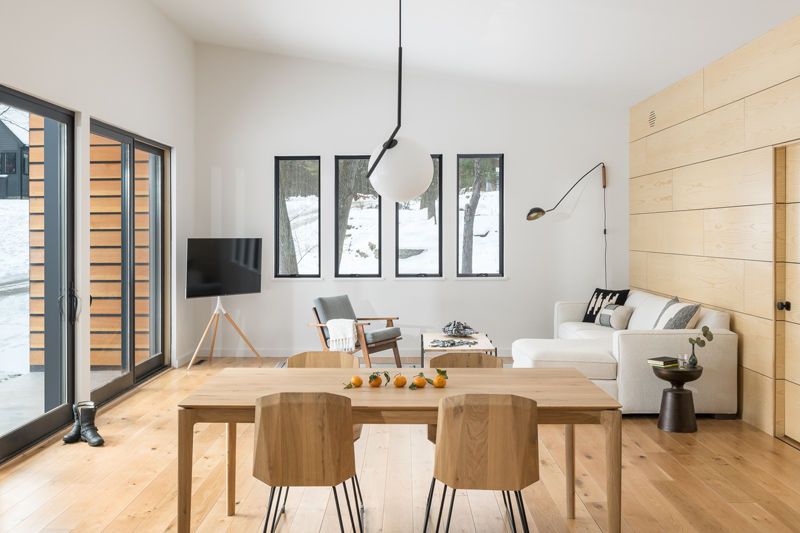
Sean describes the style of the Weybridge home as “modern, with Scandinavian influences,” and says his own personal stylistic preferences tend to lean towards “Mid-century modern.” Sean says that his original vision for the home was to create an open and inviting space that was “clean, crisp, and easy to deal with. We wanted to create a model that was cost-efficient, but still had some beautiful details. Oftentimes, the cheapest modular homes are made with plain and simple drywall and cheap finishes in the kitchen. We went somewhere in the middle, and did some modern plywood panel details on the walls. We didn’t use the cheapest plywood on the market, but it was reasonably-priced ash veneer that we finished ourselves at our workshop. We also did some matching rolling barn doors with natural paneling for the closet in the front hallway that gave it a nice countrified feel. For the kitchen area, we integrated a custom-made wooden island alongside some medium-density fiberboard cabinets that we dyed black to provide a nice color contrast. It really gives the room some richness and depth. The remainder of the wooden features in the kitchen are made out of white oak. It all ties together very nicely without breaking the bank.”

Other notable attributes of the house include its bank of southward-facing glass windows, its outdoor open-air carport that sits under an outside wooden overhang, and its starkly-modern metal roofing and siding. According to Sean, the home is insulated and constructed in a way that provides optimum energy efficiency. “The entirety of the building is externally insulated. There are fourteen inches of cellulose insulation in the roof and five and a half inches of cellulose insulation in the walls. The boards have insulation all the way to the outside. We also use an innovative air-sealing process called ‘AeroBarrier’ to further seal the house. We aerosolize a sealant into the air during the build process, and it fills all of the cracks with a pressurized fan. This whole house is sealed incredibly tightly. It doesn’t leak any heat in the winter. There is a standardized system for measuring air leaks in a house that uses a measurement unit known as ‘ACH50,’ or ‘Air Changes per Hour at 50 pascals.’ A typical home might leak at a rate of around 15 ACH. This home was measured at 0.4 ACH, which is incredibly low. It just goes to show how energy efficient and well-insulated it is. The home also features energy recovery ventilation that runs full time, acting as a mechanically-regulated leak that circulates air and recovers any heat as it leaves the house.”
Sean says that one of the most important things to take into consideration in any building project is the range of functions that the home is going to serve. “One of the most challenging things about building a successful mass-produced pre-fabricated home is having to create something that can work well in a wide range of circumstances. For me, personally, I intentionally built this home on a property where I already had another house built for me, my wife, and my three children. I knew that this smaller-model house was not going to be able to accommodate my family’s needs. Ideally, in the future, we’re going to be able to create standardized models for these pre-fabricated home homes that come in various different sizes that can accommodate a wide range of family units and functions. Whenever we work with our clients on high-end custom build products, we make sure to extensively consult with them to get an honest picture of the kind of space they need. Before we can begin the build, we need to know that the final product is going to allow them to be able to easily perform the functions that they need to be able to truly enjoy their daily lives. With these newer pre-fabricated homes, we want to translate that same perspective of applied logistics and practical objectivity into the creation of design templates that can work for a wide range of potential circumstances and living situations.”

Although Silver Maple Construction’s new pre-fabricated home design venture presents an entirely separate set of challenges, Sean says he relishes the fulfillment that comes from overcoming obstacles and solving problems as they come his way. “I am one of the few lucky people who gets
to spend every day working at a job that I love. I started out my career as a carpenter. These days, I’m morphing into my hybrid role of businessman-carpenter. As we move forward into the future, I’m blessed to still be able to turn around at the end of every day and look back at the work that I’ve done with a smile on my face. It’s been an incredible experience building Silver Maple Construction into the company that it’s become today, and I’m excited to branch out and grow our reach even further with these innovative new pre-fabricated home designs.”